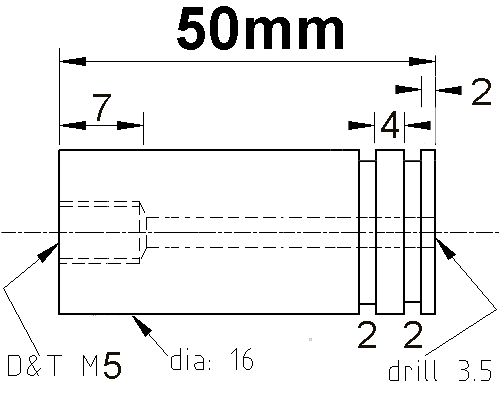
The extra 15mm of length is to clear the skate bearing carriage this is the only part where I have used a specialist tool a micro lathe.
It was to make things like this that justified my purchasing a lathe after seeing Nopheads lathe.
This lathe is the next size down making it < half the price of Nopheads you can see full details on Bodgeitquicktools blog.
This the first time of ever using a Fixed steady on any lathe. I soon realized I needed to lubricate the brass fingers so popped a drop of extra virgin oil which did the trick of stopping the horrendous screaming noise.
It was a much safer result as the Parting off tool finished the final part of its cut.
I used the parting off tool to make the two slots for the retaining cir-clips that hold it onto the X carriage.
As I forgot to to buy a center drill I used a 2.8mm wood drill first then drilled out the 3.5mm with a standard drill. Peek is a very nice material to machine much nicer than PTFE.
As I will be using welding tip for my extruder barrel the threaded part only needs to be drilled out to 4.2mm and 7mm deep for it to be tapped for a 5mm thread that the welding tips have. In my last extruder I used a B&Q welding tip
In this extruder I'm using the 5mm shorter Halfords 0.6mm welding tip. This is so I can keep the heated area as small as possible. I don't know if this is a good idea or not. I remember seeing several mentions of minimizing the thermal mass of the extruder head.
Thus with a heated barrel that is only 18mm long and 5mm diameter this extruder will have a very low thermal mass.
Its all ready to be trial fitted onto the X carriage before I use my last length of Ni-chrome wire making the heating element. I have plenty of the 16mm Acrylic block used by hobby stampers to stick their home made stamps on to press into ink and stamp all sorts of stuff with wording or outline pictures on cards journals or scrapbooks. Now there's an Idea printing custom stamps for scrapbookers and the like with Mendel.
Anyway as it is nice and see-through and its plastic its the ideal material to make the extruder block out of as you can see the holes inside it as you are working..
7 comments:
It might be worth considering using rod stock with a greater diameter than you need and turning it down to the needed OD but leaving a flange on the top end.
THis could save you a circlip but more importantly will give you a nice flat surface for your barrell to sit upon.
The top circlip could make it a little wobbly/off centre.
Having said this, most excellent. I like seeing extruder parts made on a lathe.
I think someone has started experimenting with RepRapable micro lathes. It should'nt be long before mini drill presses etc follow along too.
Its really nice. Im thinking along the line, to fix the PEEK rod with two screw on its side to prevent rotating.
Best regards,
Laszlo
http://blog.arcol.hu
@ AK47
Thank you for your suggestion.
Unfortunately what I have to hand is all I can use.
We were both made redundant from Sony Ericsson in March, not much work for those our age. After 38 years of paying NI no weekly refund ~ my forth occasion of no refund with redundancy every 9 years or so. Hence all the preparations to become self sufficient by July this year when Mortgage protection insurance runs out.
@ Laszlo k
I've not decided how to stop rotation yet. Currently it is a very tight fit. As the 16mm Peek is over sized by almost 1mm.
Very nice work Bodgeit! I've got some welding tips for extruders as well, what diameter have you drilled out your welding tip to?
It was supposed to be 3.5mm as I have used in the othersthough at the time I had mislaid the 3.5mm drill. So I used a 9/64" drill which is in fact 3.6mm I don't think the extra 0.1mm will make too much difrence.
Sorry to be exact 9/64" is 3.571875 mm
So only 0.07185mm different
Very nice blog keep it up
Pvdf sheet
Cryogenic seals
Anti-extrusion ring
Spring energized seals
Pctfe
Peek rod
Post a Comment