On the X axis these problems were:-
- Stepper motors too small to drive weight
- Home brew stepper motor controllers more expensive to buy than Zacks RRRF full kits.
- 5mml studding had too much flex was hard to buy perfectly straight straight lengths.
- Alignment of Stepper motors to studding drive is very difficult.
- Buy Stepper motors from Bits from Bytes - Excellent dual ended drive shafts.
- Buy all future electronics as complete kits from Zack at RRRF nice and easy.
- Upgrade studding from 5mm to 8mm re arrange the structure to accommodate 8mm.
- Improvise a drive linkage tried using tried springs, clear hose pipe, then used the holes left from a hole cutter which was refined to using big washers, nuts and 60 Amp chock block.
From Blogger Pictures |
Motor mounting blocks with captive nuts the large hole is 25mm the four smaller holes 5.5mm they are counter bored with 8.5mm to a depth of 2.5mm the plywood is 6mm thick.
A picture of the x axis drive its using the MDF motor couplings made from scrap floor laminate you can see how i needed to cut a slot in the base plate to accommodate the 8mm drive and bearings.
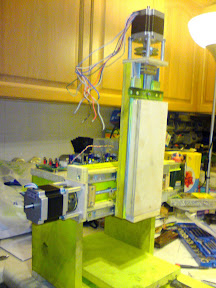
The Y Axis in close up detail motor drive coupling and bearing shown with the picture of the Y and Z axis to the right.